Home » Posts tagged 'concrete contractor'
Tag Archives: concrete contractor
Environmentally Sustainable Building With Concrete
McKinney Concrete is a ubiquitous part of the built environment. You’ll find it in the sidewalks and roads you walk on, and in your building’s foundation.
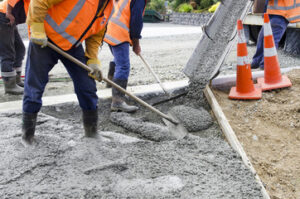
It’s a strong material. Each square inch of concrete can hold up to 3,000 pounds of pressure!
Though concrete has only four ingredients, there’s a lot of complexity in choosing the right mix for a particular purpose. That process is known as “mix design.”
Concrete has incredible strength, which makes it ideal for constructing load-bearing structures like buildings and bridges. It is also fire-resistant, which is a crucial feature for structures that will be used by people or vehicles on a regular basis. Unlike steel, which requires extreme heat to mold into desirable shapes, concrete can be formed into desired shapes with relative ease and is resistant to corrosion, weathering and other natural phenomena.
In order to make concrete strong, it is composed of aggregates (typically sand and gravel), cement paste, and water. When the concrete is mixed, a chemical reaction takes place which causes the components to bind together in a rock-solid mass. The strength of concrete is typically measured by its compressive strength, which is determined by conducting a cube or cylinder test. The higher the compressive strength, the stronger the concrete.
Concrete’s ability to resist compression is due to its compound structure, which gives it exceptional tensile strength. To increase its tensile strength, reinforced concrete is used by adding steel bars or meshes within the concrete mixture to provide additional resistance against bending and cracking.
The quality of concrete is largely dependent on the type and quantity of aggregates used in the mix, as well as the amount of cement and water. The aggregates in concrete can be either coarse or fine, and must be free from admixtures such as soft particles or vegetable matter. Aggregates are sourced from rivers, lakes and seabeds, and are crushed to form the fine or coarse concrete.
The concrete’s workability is also determined by its water content, with higher amounts of water resulting in easier concrete to place into forms and around reinforcements. However, too much water can cause the concrete to lose its strength by reducing its hydration rate.
Incorporation of supplementary construction materials, such as fly ash, slag or silica fume, can help improve the concrete’s sustainability by decreasing its environmental impact. Silica fume, for example, enhances the concrete’s early-age strength development by promoting pozzolanic reactions, while fly ash reduces ozone depletion and provides improved earthenware permeability [71]. By combining the beneficial effects of these SCMs, their use dilutes the drawbacks associated with each individual material.
Durability
Concrete is an incredibly durable material, particularly when properly designed and built. Concrete structures such as the Pantheon in Rome have been in service for over 2000 years and show no signs of degradation. When compared to wood framed buildings, concrete is a safer option for public and commercial use due to its ability to withstand the impact of earthquakes and other natural disasters. Concrete’s durability also saves its owners money by eliminating the need for sacrificial layers or shorter designed life structures.
Concrete’s durability is primarily the result of its resistance to environmental factors such as freeze/thaw cycles, chemical attack, corrosion and abrasion. If a concrete structure has not been designed to take these elements into account, then it may fail within a short time period. Fortunately, engineers are now aware of the importance of designing for durability and are starting to incorporate these factors into their specifications.
The most important aspect of a durable concrete mix is to ensure that it has the correct water content. The amount of water required is determined by the exposure class (wet or dry) to which the concrete is designed to resist. The design code also provides standard prescriptions for the w/c ratio, cement content and the aggregate type and size.
It is also important to ensure that the concrete is properly cured. The curing process involves maintaining a proper temperature and moisture level in the concrete to promote hydration and increase strength. This is especially important in the case of wet concrete, as a failure to do so can lead to premature cracking and spalling.
The incorporation of supplementary cementitious materials (SCMs) such as fly ash, slag and silica fume can enhance a concrete’s durability by filling pores, refining the pore structure and reducing permeability. These ingredients can also improve workability and reduce the need for additional water. In addition, a proper placement technique is essential to ensure that the concrete is free of voids and rock pockets. This will allow for the proper hydration of the concrete and will prevent damage to steel reinforcement by the entrapment of air.
Flexibility
Concrete is a tough building material that can be formed into various shapes and sizes at construction sites. Its most basic ingredients are aggregates, cement and water. It is also a popular choice for the foundations of buildings and bridges.
Engineered concrete can be made to bend without fracturing using special techniques. This is referred to as flexible concrete or ECC. The flexibility of this type of concrete can help to make buildings more earthquake-proof, and roads more durable. It can even reduce the damage caused by heavy vehicles.
To make flexible concrete, some of the typical ingredients found in regular concrete are replaced. The coarse aggregate is eliminated, and more fibers are added. The concrete is then mixed with a plasticizing agent, which makes it easier to work with. This type of concrete can be made on site, or it can be pre-mixed in a factory and then delivered to the construction site in a ready-mix truck.
During the mixing of concrete, water is used to create a paste that binds the aggregates together. The amount of water used is important, because if too much is added it can cause the concrete to become stiff and difficult to work with. The right amount of water promotes a chemical reaction known as hydration that helps the cement adhere to the aggregates and creates a strong, resilient structure.
One of the key components in concrete is calcium silicate hydrate, which has the ability to withstand high temperatures. It can withstand up to 910 degrees Celsius, which is well above the melting point of steel. This means that it can protect structures from fire damage by absorbing and holding heat until they can be safely evacuated.
Concrete is one of the most common building materials on the planet, and it is also one of the most environmentally damaging. It produces around 6-7 percent of the world’s greenhouse gases, contributing to global warming. However, researchers at the University of Michigan have developed a new form of concrete that is both greener and more flexible. This new concrete is made from a combination of natural ingredients and recycled waste products, and it uses less water than traditional concrete.
Environmental Impact
Concrete is a vital building material but its production is responsible for over 8% of annual anthropogenic greenhouse gas (GHG) emissions worldwide. This is primarily due to the energy used in producing cement, but also because concrete production leads to air pollutant emissions during transport and use. As demand for concrete continues to increase and existing infrastructure deteriorates, the need for environmentally sustainable construction techniques becomes more important.
To minimise environmental impact, the concrete industry is exploring new processes and materials that can replace traditional concrete with more eco-friendly alternatives. These include using recycled concrete, incorporating alternative aggregates, and utilising renewable energy during construction. These developments have the potential to significantly reduce resource extraction and energy usage. However, these alternative materials still require extensive research and development to become economically viable.
Currently, the majority of concrete is produced by combining aggregates with water and cement in a factory. This produces a mixture that can be poured into any shape and then allowed to set. However, a significant amount of water and raw materials are needed to produce just one cubic metre of concrete.
This is a significant source of waste and contributes to the high GHG emission levels associated with concrete production. Furthermore, quarrying of aggregates often involves the use of diesel vehicles and equipment that emit air pollutants. Moreover, the use of raw cement in concrete generates additional air pollutant emissions. The development of green concrete, which uses industrial waste to replace up to 25% of the cement content, may offer a more environmentally sustainable alternative.
A computational life cycle assessment (LCA) model was developed and tailored to the Australian context, assessing impacts of different concrete types across key stages of the life cycle: raw materials extraction, production, transportation, utilisation and end-of-life recycling. This model incorporates regional datasets and adheres to international standards, ensuring transparency, reliability, and applicability in the local context.
The results show that a concrete with 40% fly ash instead of cement has a lower carbon footprint than conventional concrete at the same strength level, but higher substitution rates result in even greater reductions. The inclusion of supplementary cementing materials (SCMs) such as silica fume and blast-furnace slag further decreases the impact of concrete on ecological metrics, with a reduction in acidification and freshwater aquatic ecotoxicity.